Blog
Our blog is an extension of the expert guidance you receive every time you speak with one of our advisors. From industry trends to essential tax and audit resources, you’ll gain insights to power your business dream.
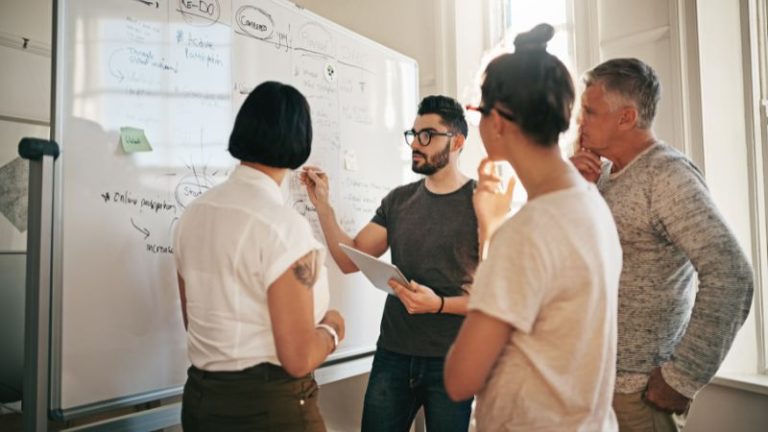
Why Growing Creative Agencies Hire Fractional CFOs (and When You Should Too)
Discover how fractional CFOs help creative agencies scale profitably. Improve...
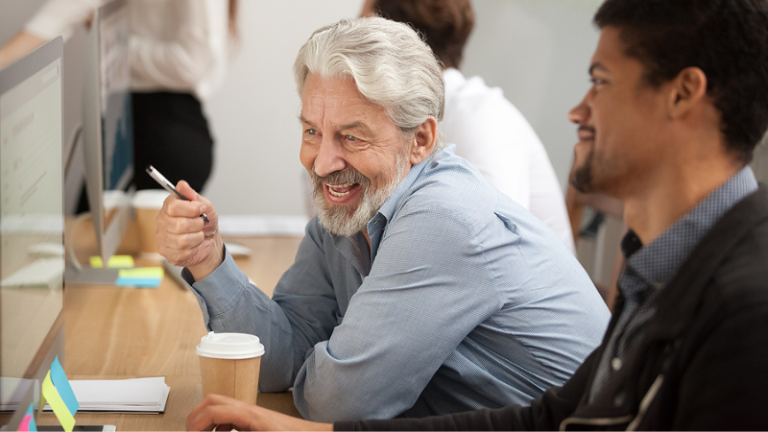
"I’m Going to Retire!" — Why You Shouldn’t Wait to Start the Replacement Search
Don't suffer through a rushed hiring process to replace retiring employees. A...
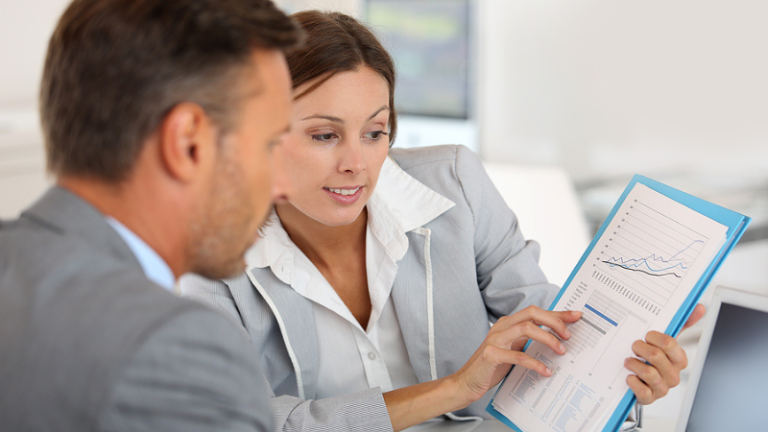
Strengthen Your GLBA Compliance with an IT Security Risk Assessment
Risk assessments for financial institutions demand forward-thinking insights ...
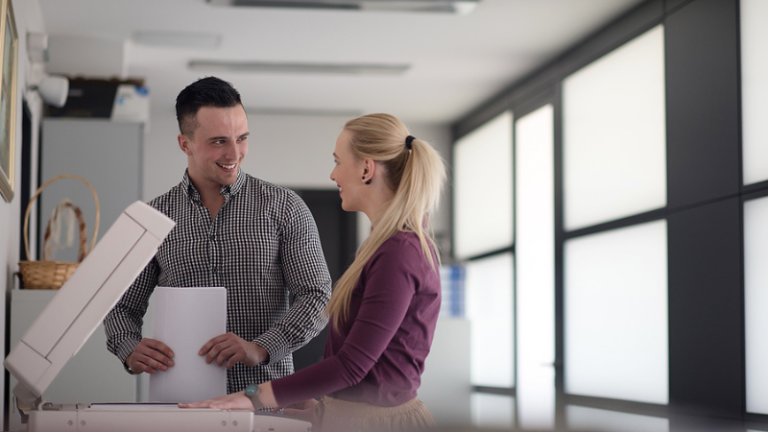
Microsoft Universal Print – Licenses, Requirements and Managing with Intune
Microsoft Universal print enables centralized management for IT administrator...
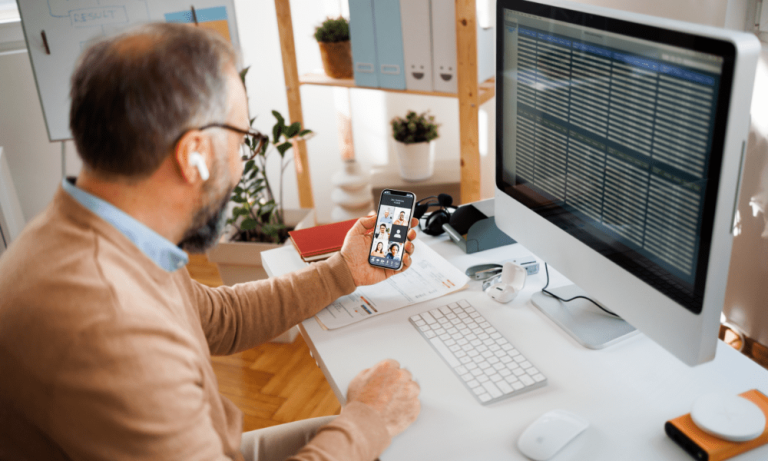
An Employer's Guide to Multi-State Payroll Tax Withholding for Remote Workers
Remote workers have become a staple of the workplace, but hiring out-of-state...
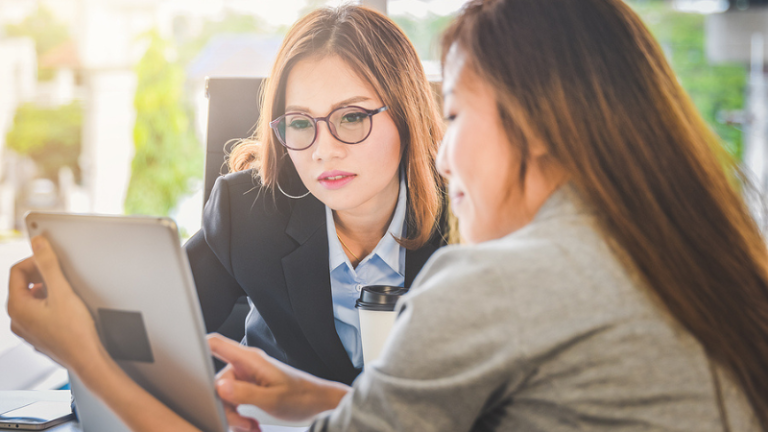
Why a Fractional CFO Might Be the Best Hire You Never Made
A fractional CFO is a financial expert with years of experience who provides ...
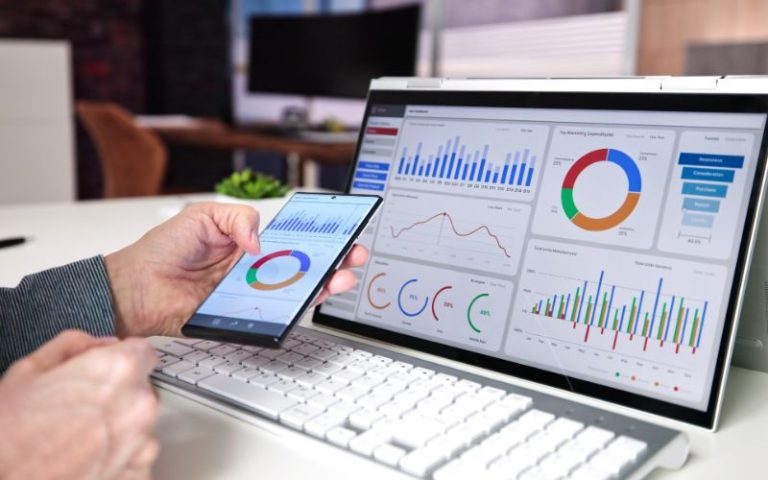
Set Effective Transportation KPIs and Financial Best Practices for Your Transportation Company
Discover key transportation KPIs and financial best practices to boost profit...
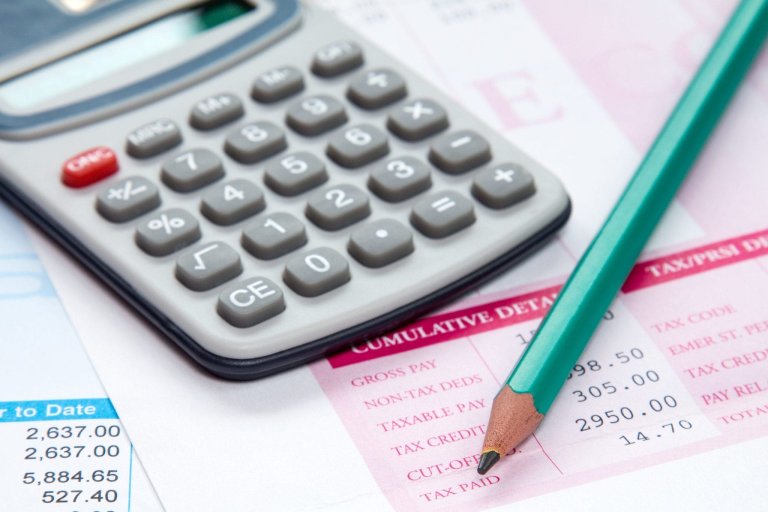
Employer Payroll Tax Obligations When Employees Work Out-Of-State
Out-of-state workers have become more common as some workplaces embrace remot...
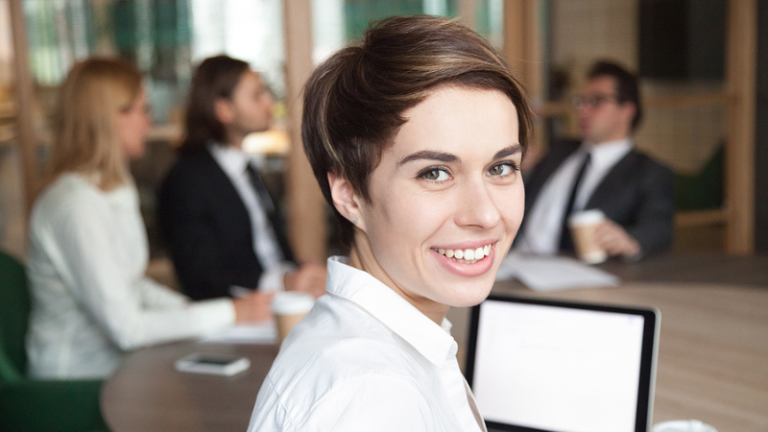
Types of Business Valuation Methods: An Overview
If you’re making important business decisions, it’s critical to understand th...
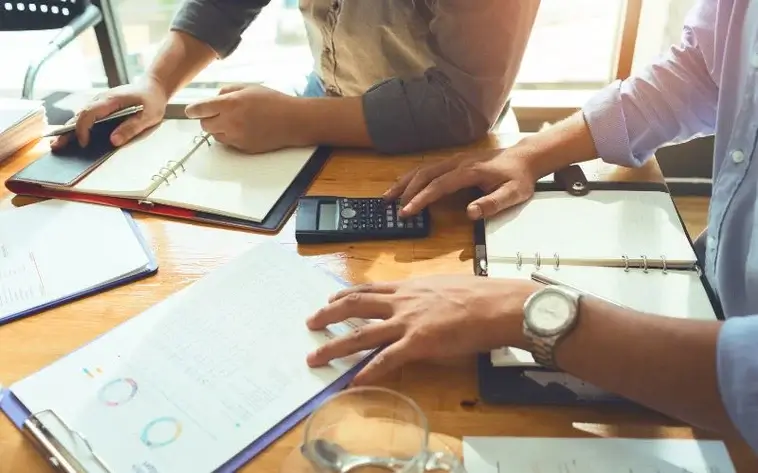
What is a Virtual CFO, and What Does a Virtual CFO Do?
A virtual CFO (aka virtual Chief Financial Officer, outsourced CFO, or part-t...
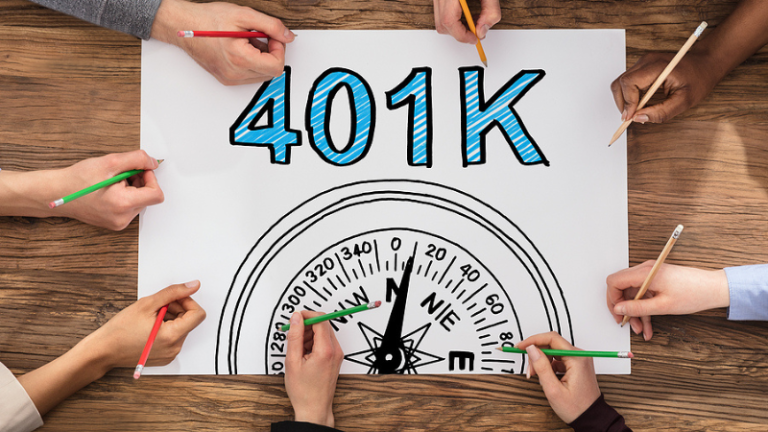
Plan Sponsor Council of America Annual Survey Reveals Secure Act 2.0 Impact on 401(k) Planning
The latest 401(k) survey from the Plan Sponsor Council of America highlights ...
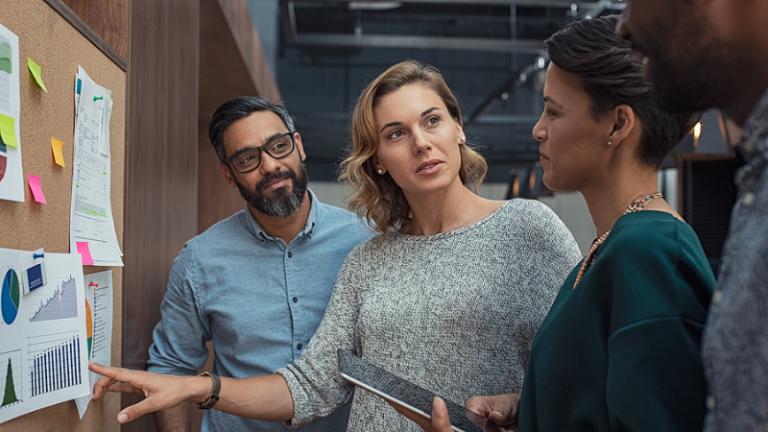
What Is a Financial Maturity Model, and Why Do You Need One for Business Growth?
At a basic level, a maturity model is a way to assess a business’s current pe...
Be the first to know
Subscribe to our newsletter and receive the information that matters to you.
Talk To Anders
We do more than solve problems – we help you sleep better at night.